Script to make same direction in path
The chain link we tested in the tensile testing machine has one design flaw. When sliced using Cura, the inner wall of the chain link is printed clockwise and the outer wall is printed counter clockwise. This resulted in a specific point on the chain link on which the fiber is not continuous but turns around. As a result, all links printed with fibers broke at the location of these turns.
To make our print stronger, python script was used. This script analyses the gcode and determines whether or not the path is clockwise or counter clockwise. If it is counter clockwise the program reverses the printing direction.
Reversing the printing direction proved a little harder than expected. This was because the E values in the gcode first had to be changed into a value for only that distance (since E values in gcode represent the total extrusion) before they could be moved around. Also the G0 (travel moves) commands had to be moved a little, since the final G1 (printing move) command per round ends up at the same position as the G0 before that round. If the order is reversed, the first G1 command moves the nozzle to the position it is already in while extruding material. This was solved by turning the coordinates of the G0 commands equal to the location of the first G1 command per round instead of the last.
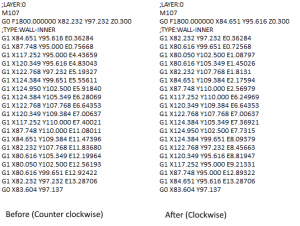
A part of the used gcode file is shown before and after running it through the script. The swap of lines can be seen.
The G0 command is needed to make this script work but can later be removed using the other python script.
Final Test
For our final print we chose the next specifications:
- Length: 50 mm
- Thickness: 8 mm
- Insider radius: 7.5 mm
- Outer radius: 20 mm
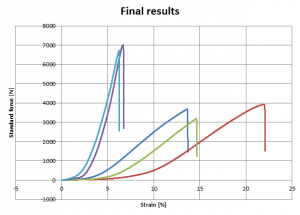
Light blue (6731N, 686kg) and purple (7017N, 715kg): Chain link with fibers. Dark blue (3691N, 376kg), green (3203N, 326kg) and red (3930N, 400kg): Chain link without fibers.
The chain links with fibers broke at an average force of 6874 N (700.7 kg). The one without fibers broke at an average force of 3608 N (367.8 kg). The one with fibers is 1.9 times stronger then the one without fibers.